process and product quality assurance process area ,how to check quality assurance,process and product quality assurance process area,The Process and Product Quality Assurance process area involves the following activities: Objectively evaluating performed processes and work products against applicable process descriptions, standards, and procedures; Identifying and documenting noncompliance issues Tags: original nike, nike real vs fake, authentic vs imitation nike, genuine versus rip off nike, nike real or fake, vopt, nike spot fake, nike legit check, legit vs counterfeit nike, authentic vs fake nike, original versus fake nike, nike amazon, nike ebay, nike ali express, nike 2019, nike real or fake, nike cr7, authenticate nike, baniya bazar uttam nagar, baniya bazar delhi, cheap shoes in .
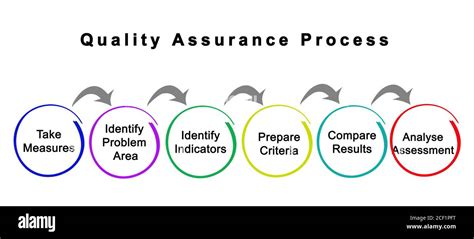
Quality Assurance (QA) is a critical aspect of any project or product development lifecycle. It encompasses various processes, methodologies, and procedures that ensure the final product meets the required standards and quality expectations. In this article, we will dive deep into the Product Quality Assurance (PPQA) process area, exploring its significance, examples of QA processes, methodologies, how to check quality assurance, and the comparison between product and process quality management. Additionally, we will explore how to perform quality assurance and what constitutes quality assurance programs.
1. Introduction to Quality Assurance
Quality assurance (QA) refers to the systematic processes and procedures that ensure a product, service, or system meets the specified requirements and standards. It helps prevent defects or errors during the development or production stages by enforcing defined practices and controls. QA is not only focused on the product itself but also on improving the overall process, ensuring efficiency, consistency, and predictability in the workflow.
Product Quality Assurance (PPQA) specifically supports the delivery of high-quality products and services by providing project staff and managers with appropriate visibility into the quality of the work being produced. PPQA is designed to ensure that quality assurance processes are adequately followed throughout the project lifecycle, from requirements gathering to product delivery.
2. The Role of Product Quality Assurance (PPQA) in Project Success
Product Quality Assurance (PPQA) serves multiple functions in ensuring the successful delivery of high-quality products. The main goals of PPQA are to:
- Ensure Compliance: Ensure that all processes are compliant with industry standards, regulations, and client-specific requirements.
- Prevent Defects: Implement early detection mechanisms to prevent the introduction of defects during the development cycle.
- Continuous Improvement: Identify areas for improvement in both processes and products and provide recommendations for optimization.
- Transparency: Provide visibility to stakeholders regarding the project’s quality metrics, risks, and performance.
- Customer Satisfaction: Ensure the end product meets or exceeds customer expectations.
3. Key Quality Assurance Processes
The quality assurance process involves various steps and activities to monitor and evaluate the development process. Below are the primary categories of quality assurance processes commonly used in product and process management.
# 3.1 Quality Assurance Processes Examples
Here are some examples of key quality assurance processes:
- Requirements Analysis: Ensuring that requirements are well-defined, clear, and unambiguous before the project begins. This process helps in identifying potential gaps in the requirements early on.
- Design and Development Reviews: Conducting regular design and code reviews to ensure the solution architecture, design, and code are aligned with requirements and quality standards.
- Testing and Validation: Implementing functional, integration, and user acceptance testing to validate that the product performs as expected and satisfies customer needs.
- Audit and Compliance Checks: Performing internal and external audits to verify adherence to quality standards and regulatory compliance.
- Metrics Collection and Reporting: Collecting data on quality metrics (such as defect density, defect resolution time, etc.) to measure and improve quality levels.
- Corrective and Preventive Actions (CAPA): Identifying recurring problems and implementing corrective measures to prevent future occurrences.
# 3.2 Quality Assurance Processes and Methodologies
Quality assurance methodologies guide the practices and approaches used to assure the quality of the product and processes. Some of the most widely adopted QA methodologies include:
- Agile Quality Assurance: In agile development, quality assurance is integrated into each sprint or iteration. QA activities such as testing, reviews, and improvements are conducted in parallel with development to ensure that quality is maintained throughout the process.
- Waterfall Model: In the traditional waterfall model, QA activities are typically performed after the development phase, where testers validate the product against defined requirements. However, this model is less flexible compared to agile and often leads to later detection of issues.
- Total Quality Management (TQM): This methodology emphasizes continuous improvement and customer satisfaction. It involves every team member in the quality process and focuses on improving processes and product quality across all departments.
- Six Sigma: Six Sigma aims to reduce defects by identifying and eliminating sources of variation in processes. It uses statistical methods to improve process efficiency and ensure product quality.
- Lean Manufacturing: Focused on reducing waste and improving process efficiency, Lean methodologies are used in manufacturing to streamline processes and enhance product quality.
# 3.3 Quality Assurance Processes and Procedures
To maintain a consistent approach to quality, organizations define clear quality assurance procedures. These procedures describe specific tasks and activities for project teams to follow in order to ensure the quality of both products and processes.
Some typical quality assurance procedures include:
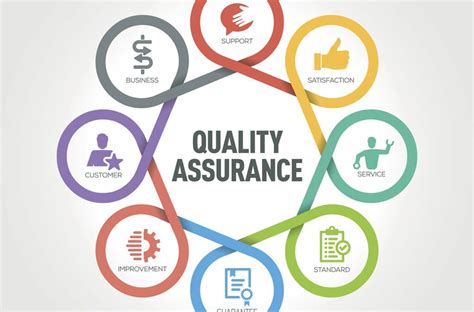
process and product quality assurance process area Discover discount designer clothing, shoes, handbags, jewelry and more at Saks OFF 5TH. Save up to 70% off top brands with free shipping on orders over $49.
process and product quality assurance process area - how to check quality assurance